In other words, the AQL standard gives the number of products to inspect & the maximum number of defects the buyer is willing to accept.
In order to optimally use the AQL standard, the buyer must first set two critical tasks:
- Build a clear and exhaustive list of checkpoints,
- Finalise the quality levels expected from the production.
We will see below how to do this. But first let’s see what is the AQL.
How does the AQL work?
Why do we use the AQL?
1. It limits waste
2. It reduces time and cost
Let’s see what it takes to inspect 100% in terms of time and cost:
For example, you order 3500 computer displays from a factory in Shenzhen. It takes 2 minutes to perform all the required tests on ONE display. Totally, it takes 117 hours to test 3500 computer screens. That’s 15 days of non-stop inspections (8 hours a day). Inspections costs are based on man/day, so if a single inspector asks for $349 ; for 15 man/day, expect to pay around $5235, that’s a huge amount compared to the price of the goods. Furthermore, not many buyers are willing to wait 15 more days after production to ship their products. And no factory will accept to store the goods and monopolise factory workers for 15 days of inspections after production.
The AQL comes handy, allowing to check a sample size of the production within a day or two while keeping a clear view of the quality.
It’s also financially much more interesting for the buyers.
3. why not use a fixed percentage then?
How does AQL look like?
How to use the AQL tables?
1. Table A: setting the sampling size
A. Lot size = order quantity
B. General inspection levels
Choose General Inspection Levels if your checkpoints require tests on all of the sampling size. There are 3 levels going from smaller (I) to bigger (III) quantity. You can choose the inspection level according to your budget and the risk you’re willing to take. Note that most of the inspections in China use Level II.
Lower inspection level means cheaper cost but higher risk.
Higher inspection level means higher cost but more clarity.
C. Special inspection levels
D. Sample size code letter
2. Table B: collecting the accepted and rejected quantities
A. Sample size
B. Acceptance quality levels
C. AC= accepted defect quantity
D. RE = rejected defect quantity
E. Vertical arrows
Defining the checkpoints
The best practice asks buyers to define all the checkpoints before the mass production starts. That way, you make sure the factory understands your expectations in terms of quality, lowering the risk of defects during the production.
Once you have made a list of checkpoints, you may want to assign them different levels of tolerance. Inspectors classify defects in 3 categories:
- Minor: defects that are unacceptable in high quantities but generally won’t result in product returns.
- Major: defects that would likely result in product returns but don’t pose a safety risk to the user.
- Critical: defects that violate regulations or pose a threat to user safety.
Here’s how most inspectors assign Inspection Levels to defect categories:
- Minor -> AQL 4
- Major -> AQL 2.5
- Critical -> AQL 0
Let's check with a practical example
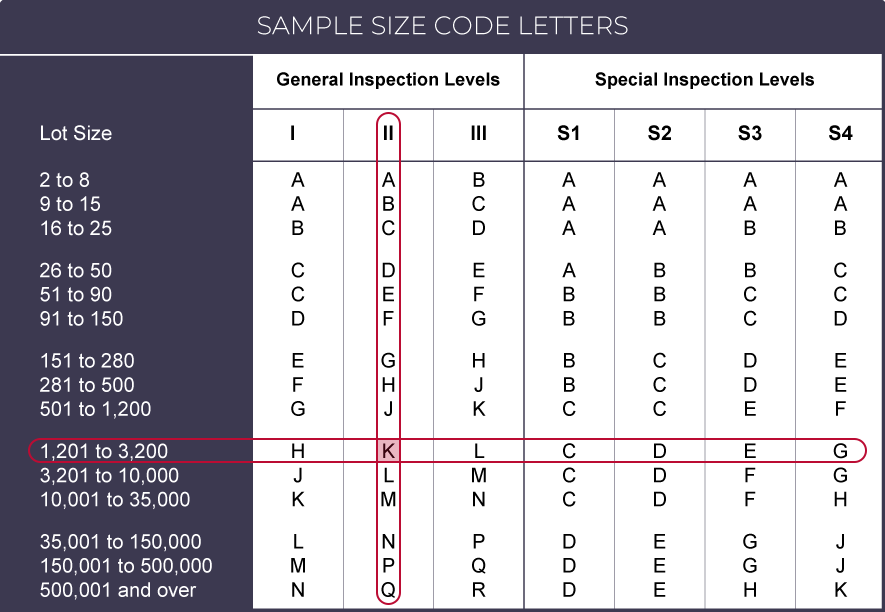
Let’s check the second table, “Single Sampling Plans for Normal Inspection”, to have concrete information regarding the quantity of inspected items and the limits for accepted and rejected defects. The letter K from the first table tells us that we should inspect 125 tablets. Our inspectors advise AQL 4 for minor defects, AQL 2.5 for major defects and AQL 0 for critical defects.
We now have a look at your checkpoints and the defects found:
- Checkpoints in minor defect category = 10 accepted defects. Refuse order from 11 defects.
- Checkpoints in major defect category = 7 accepted defects. Refuse order from 8 defects.
- Checkpoints in critical defect category = 0 accepted defects. Refuse order from 1 defect.
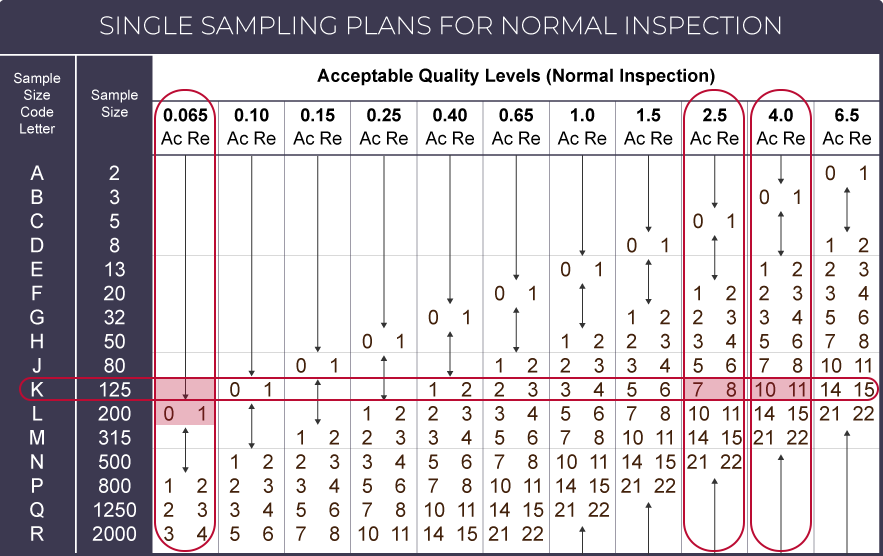
Assuming that each tablet can be inspected in 2 minutes, this inspection can be done in 1 day by 1 inspector (meaning 1 man/day).
It should be mentioned that if you want to inspect 100% of this order, it will take 11 man/days.
Is AQL enough?
The AQL standard is very useful for all the appearance defects (size, colour, etc.). Nevertheless, it does not reflect the overall quality status of your order because it does not include the inspections of:
- On-site tests for functionality, safety and performance,
- Regulations and distributor requirements.
You should not rely on the result of the AQL tests only, but on the final inspection report result, given by the inspection company.
To sum up the AQL
A word of advice from ASIACTION experts
Most of the QC companies offer a very limited assistance before, during or after the inspections. They ask you to fill in their long inspection forms (usually not very user-friendly), to prepare the booking with the factories and to follow the inspection schedule with these factories. After the inspection they usually send you an inspection report with little to no explanation. Basically, you end up all by yourself trying to decipher the report and to fix the potential problems with a Chinese factory far from you.
At Asiaction, our team in China personally helps you build up the checkpoints and their categorisation in a clear inspection sheet. We then are completely available during the booking and the inspection. We send urgent warnings if necessary during or right after the QC. After the inspection, we send you a comprehensive report and our experts are still available for any clarification.
Most importantly, ASIACTION have experts who advise and help you to resolve cases with your Chinese suppliers after the QC.
If your QC report presents defects leading to a failed status of the order, contact us to get our help on negotiation with the factories whether you prefer to have a discount, to fix the problems or to refuse all or a part of the order.