Product Inspections
We offer thorough product inspection and quality control services in China. Our team ensures your products meet all specifications through detailed inspections at every production stage. We provide comprehensive reports with HD photos and videos, guaranteeing transparency and quality assurance.
what we inspect
(included in the report)
Quantities
On site, our inspectors check that the factory prepared the agreed-upon number of products. We verify various kinds of quantities:
- Total quantity ordered/produced,
- Quantity of products packed,
- Quantity of products not packed,
- Quantity of cartons packed,
- Quantity of cartons not packed.
Workmanship & Appearance Defects
We randomly choose a number of products (set by the AQL standard) and search for visible defects. We arrange these defects in 3 categories (critical, major or minor) and the number of defects in each category will tell you whether you should accept or refuse your order.
Measurements & Tests
We check that the products’ sizes match those from your purchase order. According to the type of product, we will check its electrical power, its functions, its packaging strength, and anything specific to your product.
Products Specifications
We check that all the specifications from your purchasing order match those of the manufactured products. We test the functions, the electric power and plug, the colours and the material.
Marking & Labels
We check that all markings, printing and label match those specified from your purchase order.
Packing
We check that the packing from the factory matches your purchase order. Especially if you ordered flat packing or Mail Order Packing (MOP).
Custom Checkpoints
If you have specific needs and checkpoints, just let us know during the inspection preparation and we’ll easily add them into our process so that you get the inspection you need.
HD Pictures & Videos
We provide HD pictures of the products and of all the defects. We also include videos of different locations in the factory.
Quality Control Reports
How we operate inspections ?
all types of products
Our product inspection allow you to evaluate any production on any kind of produtc. Make sure you check your goods before shipping them out.
Everywhere in China
We have collaborators all over China able to intervene in:
Fujian, Guangdong, Hebei, Shandong, Shanghai, Tianjin, Zhejiang.
At any
moment
We go to factories:
to check prototypes, for pre-production sample check, in the middle of production, for random final inspection when all is packed
product inspection process
In 4 phases
Preparation
Study of the request by our team. Collection of your requirements and standards to be verified. Planification of the intervention.
Quality Control
Visit of an Asiaction inspector on-site. Verification of compliance with all specifications and inspection of the representative sample to ensure that it meets your requirements and the ISO2859-1 AQL standard.
Testing
Verification of specifications (product, packaging, labeling). Measurements and functional tests with an option to organize laboratory tests.
Monitoring
Control of the running production and verification that the requirements are fulfilled.
inspection
by Asiaction
English interlocutors
ensure the proper transmission of information
Involvement of 3 Asiaction agents
project manager, quality manager and inspector
Trained inspectors
to European quality standards
Advice and explanation
assistance in the preparation of the inspection plan and recommendations
Risks without
inspection
Non-compliance
colors, material, dimension, features, etc.
Dangerousness
(ex: sharp edge, nail, resistance, electrical leak, etc.)
Scam
products completely different
Chronology of Our Services
You want us to validate a potential supplier ?
We do off-site and on-site audits of Chinese companies
You need quality control on your on-going orders ?
We can operate quality control & loading supervision
You need a reliable supplier in China now ?
We can find a supplier in China for you
You want us to manage your procurement ?
We offer a complete management solution
Why Choose Us ?
Experience & Expertise
Specialist in purchasing and manufacturing processes in China since 2008.
Personalized
support
An Asiaction expert will support and follow you throughout your projects.
A team
on site
An operational office in China managed by French people.
Transparence & Integrity
Respect of our partners and requirement of a quality job.
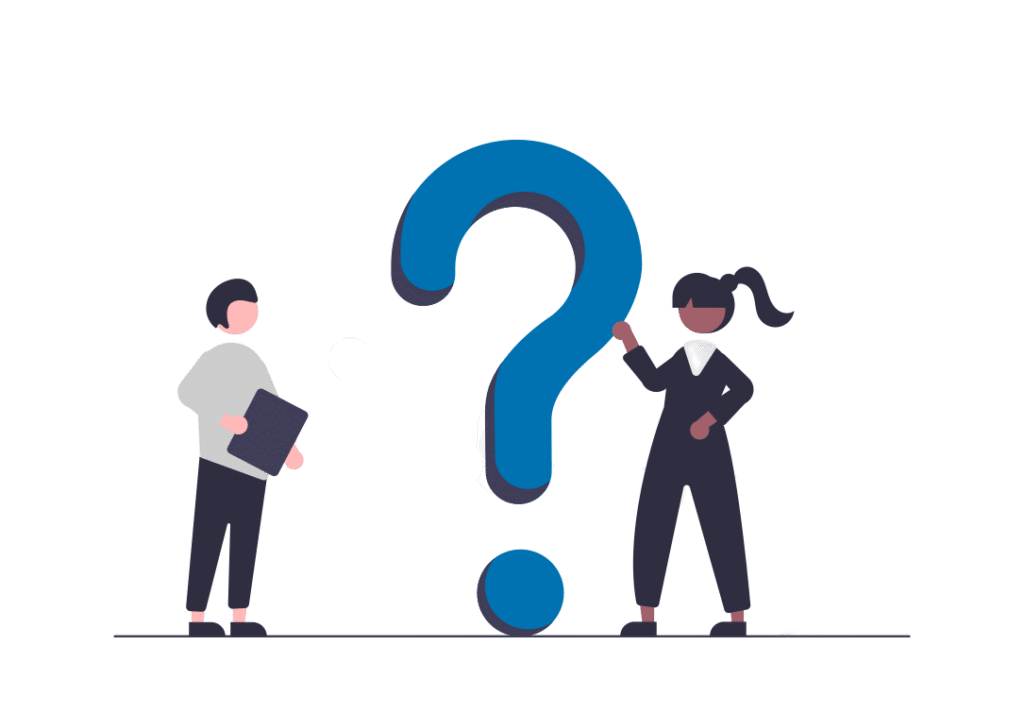
Have you heard?
We publish tips and tricks on buying in China on our LinkedIn page.
Stay update by following our page now!
FREQUENTLY ASKED QUESTIONS
ABOUT PRODUCT INSPECTION
What is a man-day?
Every inspection is performed by a number of persons over a number of days. Most inspections are made by one man within one day, that’s 1 man-day. However, it is possible that some inspections require more people and/or more time.
For example, we could send 2 inspectors to perform an inspection within 1 day, that’s 2 man-day.
Examples:
1 inspector on 1 day = 1 man-day
2 inspectors on 1 day = 2 man-day
1 inspector on 3 days = 3 man-day
2 inspectors on 2 days = 4 man-day
What is the AQL?
All about the AQL standards here.
Unless specified otherwise, we do not inspect 100% of the production. We choose a number of products randomly, based on the AQL standard. All the inspections carried out by the Asiaction product inspection team follow the process defined by the international standard ISO 2859-1 (ANSI / ASQC Z1.4-2003).
HOW TO CONTROL THE QUALITY OF A PRODUCT?
Have your goods inspected with ASIACTION before they leave the Chinese factory. An ASIACTION inspector will visit the factory at any time during the production process and will send you a complete report of his visit with pictures and videos.
We verify the product specifications that you have agreed with the factory. We also verify the industry standards.
Products can be the wrong color, the wrong material, the wrong dimensions.
WHAT ARE THE QUALITY PROBLEMS OFTEN FOUND?
Defects are the result of poor workmanship or an incorrect production process.
Defects are also the result of tests performed by the inspector to verify the general requirements of a specific product type. For example, the loading capacity of a chair or the strength of the paint. Defects may also occur during special tests you ask us to perform.
The most frequent quality problems are:
- Non-conformity of colors, materials, dimensions, functionality
- Dirtiness
- Poor finish
- Scratches
- Broken pieces
- Dangerousness: sharp edge, nail, resistance, electrical leak, etc.
WHY INSPECT PACKAGING AND MARKING IN QUALITY CONTROL?
Packing may be a specific requirement on your part, but it is also an important aspect of product safety. During transport, especially in express shipments, fragile cartons and inadequate packing will not protect the goods. The goods may be damaged before they reach the final consumer.
YOUR PRODUCT IS NOT LISTED OR YOU NEED A QUALITY CONTROL AT ANOTHER TIME?
Contact us and tell us when you need ASIACTION to intervene.
We can also build together your inspection.
WHAT IS A QUALITY CONTROL?
Quality control ensures that the goods meet the buyer's specifications. It is a process that can save you money by correcting problems before the goods leave the Chinese territory.
WHY A QUALITY CONTROL?
Quality control consists in inspecting the goods at any time during the production process to ensure their conformity before the order is shipped. This allows us to avoid non-conformity of the products to your requirements and to avoid scams.
For products coming from countries such as China, we recommend to conduct a quality control before the departure of the products. Once the goods arrive at their destination, it is too late to correct quality problems.
Following the quality control, ASIACTION will send you a complete inspection report and your goods will leave the factory only when you have given your approval.
HOW IS THE QUALITY CONTROL DONE?
The quality control (or goods inspection) is done by sending an ASIACTION inspector in the factory at any time of the production anywhere in China. Several aspects are inspected:
- Quantities
- Manufacturing and aspect defects
- Measurement and functional tests
- Product specifications
- Marking and labels
- Packing
- Special inspection points according to your requirements
WHAT ARE THE TYPES OF QUALITY CONTROL?
There are several types of quality control. With ASIACTION, it is possible to make a goods inspection at each step of the production process:
- Before the start of production
- When the production starts
- During production
- At the end of the production
- Before loading the container
- During the loading of the container
Contact our experts and schedule your quality control quickly.
HOW TO CONTROL 100% OF YOUR PRODUCTION IN CHINA?
It is possible to have the totality of your production controlled in China. ASIACTION will contact your factory and inform us about the number of inspection days needed to control the quality of your total production.