In the fast-paced world of global business, understanding supplier performance is vital for success, particularly in a major manufacturing hub like China. To have an accurate understanding and to make informed decisions, it’s essential to look into key metrics that can provide insights into the effectiveness and efficiency of suppliers. Here’s an in-depth analysis of the Top 5 Key Supplier Performance Indicators that are critical in analyzing supplier performance in China. With this comprehensive guide, explore the ins and outs of these metrics, understand their importance, and learn the best practices to monitor them effectively. Let’s get started!
1. Lead Time: Ensuring Efficiency in Production and Shipping

This indicator represents the number of days from order placement to production completion. It’s a vital aspect in the supply chain management process, especially when dealing with suppliers in China.
Short lead time = efficiency of the supplier’s production process.
In international business, lead time can significantly impact planning, inventory management, and overall customer satisfaction. Here’s why understanding and monitoring lead time is essential:
- Forecasting Accuracy: By tracking lead time, you can better anticipate delivery schedules and optimize inventory levels.
- Cost Management: Minimizing lead time reduces holding costs and potential stockouts, ultimately benefiting the bottom line.
- Supplier Selection: Understanding a supplier’s average lead time helps you make informed decisions when selecting partners.
Efficient lead time management ensures that inventory levels are optimized, reducing holding costs, and ensuring timely delivery.
2. On-Time Delivery: Meeting Expectations
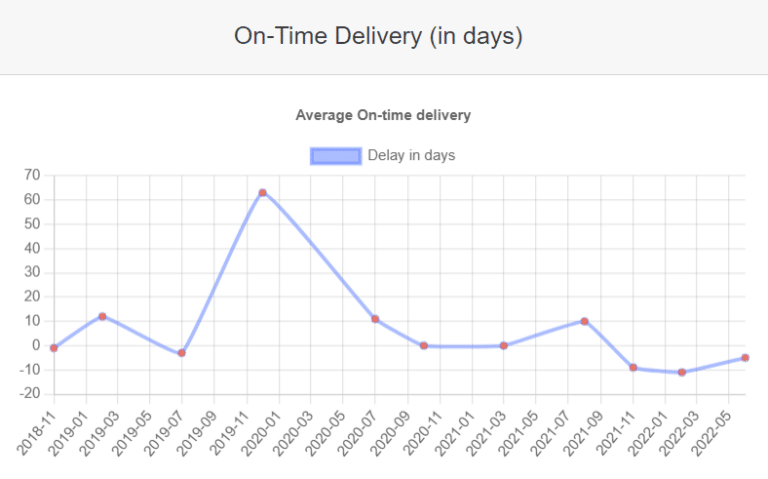
The on-time delivery signifies how consistently a supplier delivers products within the promised timeframe. It is a measure of reliability and is an essential aspect in supplier evaluation in China. This is the number of days late or early delivery.
Negative number of days = early delivery reflecting good logistics management and compliance with delivery deadlines.
- Early Deliveries: Though early deliveries might seem good, they can disrupt inventory management.
- Late Deliveries: Late deliveries can lead to stockouts and potential loss of sales.
This metric provides insights into:
- Supplier Dependability: A negative on-time delivery is a sign of a reliable supplier, enabling better planning and reducing potential disruptions.
- Customer Satisfaction: Timely deliveries can enhance customer satisfaction, strengthening relationships and ensuring repeat business.
- Performance Benchmarking: Regularly tracking on-time delivery allows for performance comparisons across various suppliers, facilitating better decision-making.
3. Non-Conformity Rate: Compliance with Standards
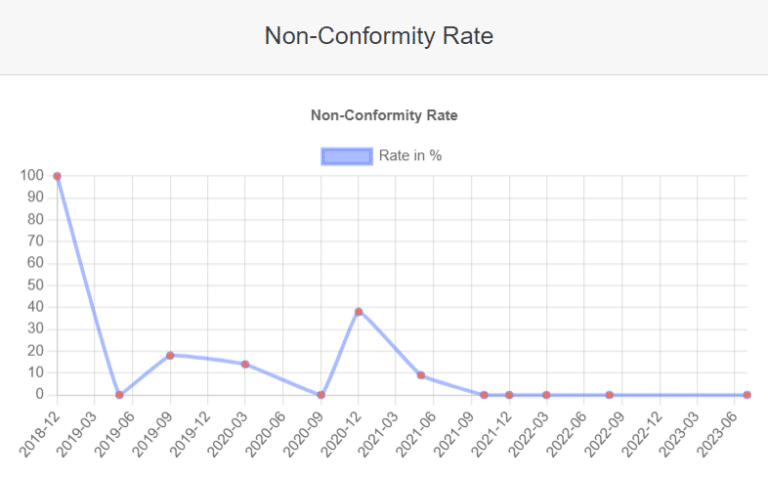
This KPI measures the percentage of products that fail to meet the specifications set out in the order. These are products which, although functional, do not meet your requirements. For example, a clothing item in the wrong color, or a machine with incorrect dimensions.
Low non-conformity rate = precision and reliability from the supplier.
Analyzing this indicator in China requires a keen understanding of both international and local regulatory norms. This metric helps in:
- Quality Assurance: Regularly monitoring non-conformity rates ensures continuous adherence to quality standards.
- Risk Mitigation: Early detection of non-conformities allows for swift corrective actions, mitigating potential risks.
- Cost Savings: Reducing non-conformities leads to fewer rejections and rework, ultimately saving costs.
Regular audits and strict adherence to quality control measures can minimize the non-conformity rate.
4. Defect Rate: A Measure of Quality Control
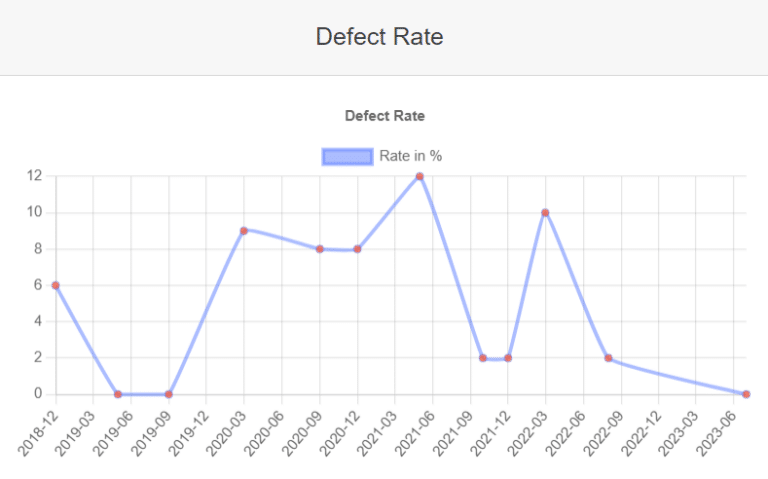
This is the percentage of defective products out of the total number of products manufactured. A product is considered defective if it has a technical or functional defect that affects its normal use. For example, an electronic device that won’t switch on, or a clothing item with a poorly sewn seam.
Low rate = good management of quality processes by the supplier, which can reduce your quality control costs.
Monitoring the defect rate is vital for:
- Quality Control: A low defect rate is indicative of consistent quality, strengthening brand reputation.
- Resource Optimization: Understanding defect causes helps in process improvements, reducing wastage, and optimizing resources.
- Vendor Evaluation: Regularly evaluating defect rates across suppliers enables better vendor selection and management.
Continuous monitoring, inspections, and working closely with suppliers can drastically reduce the defect rate.
5. Return Rate: Analyzing Customer Satisfaction
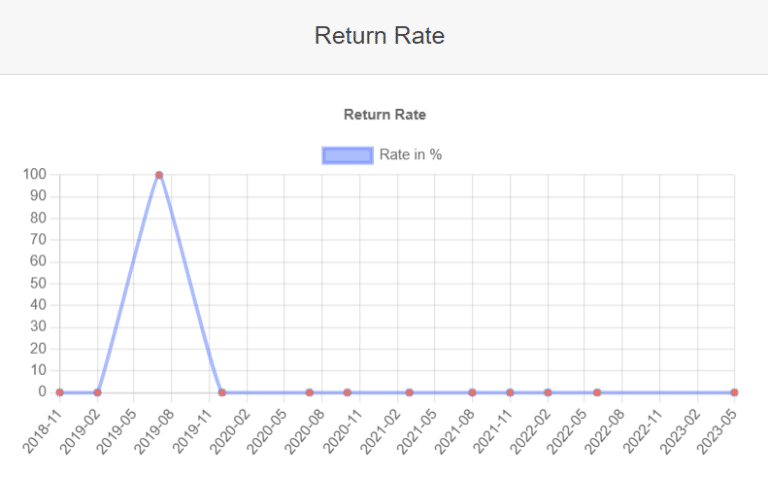
This KPI measures the percentage of products that have encountered problems during transport or after use, in relation to the total number of products ordered. It’s an indirect indicator of supplier performance in China, as it reflects on the quality and conformity of the products.
Low return rate = products meet expectations.
Analyzing this metric provides insights into:
- Feedback: Returns often reflect dissatisfaction, offering valuable feedback for improvement.
- Profit Impact: High return rates might indicate underlying issues, potentially affecting profitability.
- Product Improvement: Analyzing return reasons can lead to product enhancements.
Monitoring and analyzing return rates, followed by corrective actions with suppliers, can enhance customer satisfaction and profitability.
Conclusion
Understanding these Top 5 Key Supplier Performance Indicators provides a comprehensive view of supplier efficiency, reliability, and quality, particularly in the complex and dynamic environment of China. By carefully analyzing lead time, on-time delivery, non-conformity rate, defect rate, and return rate, businesses can ensure a smooth and effective supply chain, sustaining success in a highly competitive marketplace.
Asiaction: Revolutionizing Supplier Performance Tracking in China
For the first time in sourcing, Asiaction brings you an unprecedented enhancement to your customer experience, presenting a major innovation that transforms your customer portal.
New Functionality: Track Your Suppliers Like Never Before
Asiaction’s customer portal enables you to track all key supplier performance indicators such as Lead Times, On-Time Delivery, Non-Conformity Rates, Defects, and Returns with total ease.
Improved Performance: Everything Now at Your Fingertips
Experience improved performance with all essential metrics right at your fingertips. Never before has tracking supplier performance been so efficient and seamless.
Total Transparency: KPIs Chosen for You
With total transparency as our commitment, we shed light on your suppliers’ performance, optimizing your purchasing experience. The KPIs are specifically chosen for you, reflecting our proven expertise.
Proven Expertise: A Powerful Tool at No Extra Cost
We have been tracking supplier performance internally for years. Now, we’re offering you this powerful tool at no additional cost. Your success is our priority, and we provide the tools and information necessary for better decision-making.
Continuous Innovation: Efficient and Transparent Service for You
Asiaction is committed to continuous innovation, offering an ever more efficient and transparent service, tailored just for you. We make supplier transparency accessible to all, allowing you to optimize your supply chain management like never before.